2600mm X 5200mm Silicone Membrane for Solar Module Laminating Machine and Encapsulation Line
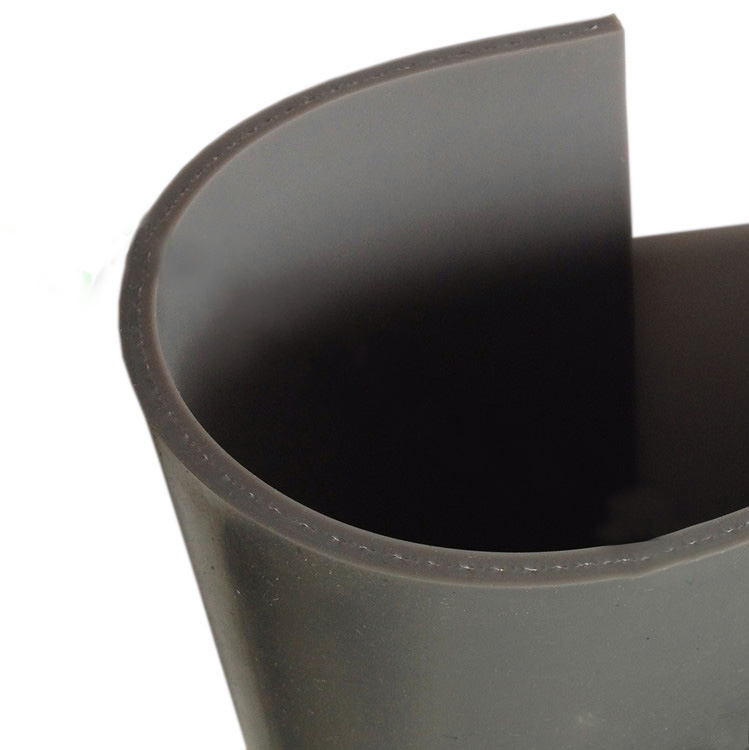
2600mm X 5200mm Silicone Membrane for Solar Module Laminating Machine and Encapsulation Line
CASIS – Asia's leading supplier for specialty silicone sheets for solar panel manufacture in the renewable energy market. Silicone Membrane for Solar Module Laminating Machine and Encapsulation Line. Although also called diaphragms, sheets, or membranes, the solar panel industry tends to use the term membrane.
Product description and advantages
• Both sides gray color and silicone materials
• Bond of the two layers cannot be separated mechanically
• High temperature aramid fabric inserted in the middle
• Constant quality thanks to quality management
• Durability results in longer machine running times and thus shorter set-up times
Standard dimensions
Width: Max up to 3800mm
Material thickness: 4 mm
Fabrication even beyond the standard width
The Second Generation KS-EXR268 lamination diaphragms are specially designed for the solar module lamination process.
Our silicone membranes are enhanced to achieve higher laminator uptime and decreased running costs.
Starting from base silicone materials, our membrane material formulation and its manufacturing process have been optimized to offer a superior product. Our solar module lamination membranes are available up to 3,050 mm wide without a splice. This offers module manufacturers with the advantage of not having seam marks visible on their backsheets created during the lamination process.
Do you need a wide silicone laminator membrane without a splice?
CASIS’s seamless lamination membrane enables module makers to produce modules up to 3,050 mm wide with no seam marks visible on the back sheet.
Features and Benefits:
-
Seamless surface up to 3,050 mm wide
-
Cycle life of over 3000 cycles *
-
High temperature resistant
-
Excellent elasticity and stability
Cycle life is dependent on set up and operating conditions.
The Second Generation KS-EXR268 Silicone Membrane
Photovoltaic modules need to withstand harsh environmental conditions for long periods – 25 years or more. One of the keys to module longevity and reliability is the lamination process, which encapsulates solar cells while attaching front and back protective sheets.
Lamination Process
The lamination process involves pumping the air out of the module layers in a vacuum chamber, heating the layers to melt the encapsulant, and pressing the layers together with a flexible diaphragm or membrane to embed the cells in encapsulant and adhere the front and back sheets. The flexible membrane is attached to the top of the vacuum chamber, and a set of valves allows the space above the diaphragm to be evacuated.
There are 3 main purposes of the membrane in the vacuum process:
-
To exert a uniform pressure throughout the solar lay-up.
-
Removal of moisture, solvents and volatiles from curing composite layers.
-
Allow encapsulant material to flow evenly throughout solar cell lay-up.
Our Main Partners :